In the realm of food processing, effective pest control stands as a paramount necessity to preempt costly shut-downs. Enter Insect-O-Cuter®, offering a meticulously designed three-phase system aimed at achieving optimal results in flying insect elimination within industrial settings. The first phase involves strategically placing units at the perimeter to intercept flying insects immediately after entry. The second phase introduces supportive Insect-O-Cutor® units along probable insect flight paths, protecting sensitive areas where contamination is a concern. The third phase places Insect-O-Cutor® units as a final interception outside crucial zones like processing and food preparation areas. The accompanying map guides the implementation of this comprehensive pest control strategy. Noteworthy considerations include the strategic placement of units in stairwells and elevators to address natural insect pathways. The provided FAQ section sheds light on various aspects, from the necessity of changing bulbs to the significance of Shat-R-Shield® bulbs in maintaining safety standards. Regular maintenance practices, including periodic cleaning, lamp replacement, and careful consideration of coverage factors, are also elucidated to ensure the sustained effectiveness of the Insect-O-Cutor® system.
In food processing environments pest control is a must, staying ahead of the game is important and necessary to avoid costly shut-downs. Below is a comprehensive three-phase system designed by Insect-O-Cuter® to offer the best results for elimination of flying insects.
Three-Phase System Design (for Industrial Application)
First Phase: (perimeter defense) units should be located in positions where they will intercept flying insects immediately after entry. If the receiving dock is covered, an Insect-O-Cutor® unit should be located on the dock to reduce the number of flying insects gaining entry through the receiving dock doors. For best results, every exterior door should be protected by locating an interception unit inside the building within 20' of the door, oriented so that flying insects must pass within 15 to 20' of the unit.
Second Phase: (back-up/supportive Insect-O-Cutor® units) should be located along the probable insect flight path—between phase I and sensitive areas, processing/manufacturing areas, packing areas, or anywhere flying insects might contact or contaminate product or cause personnel annoyance.
Third Phase: Insect-O-Cutor® units provide final interception immediately outside sensitive areas. Units located within processing/manufacturing areas, production areas and food preparation areas, and in cafeterias are considered as Third Phase.
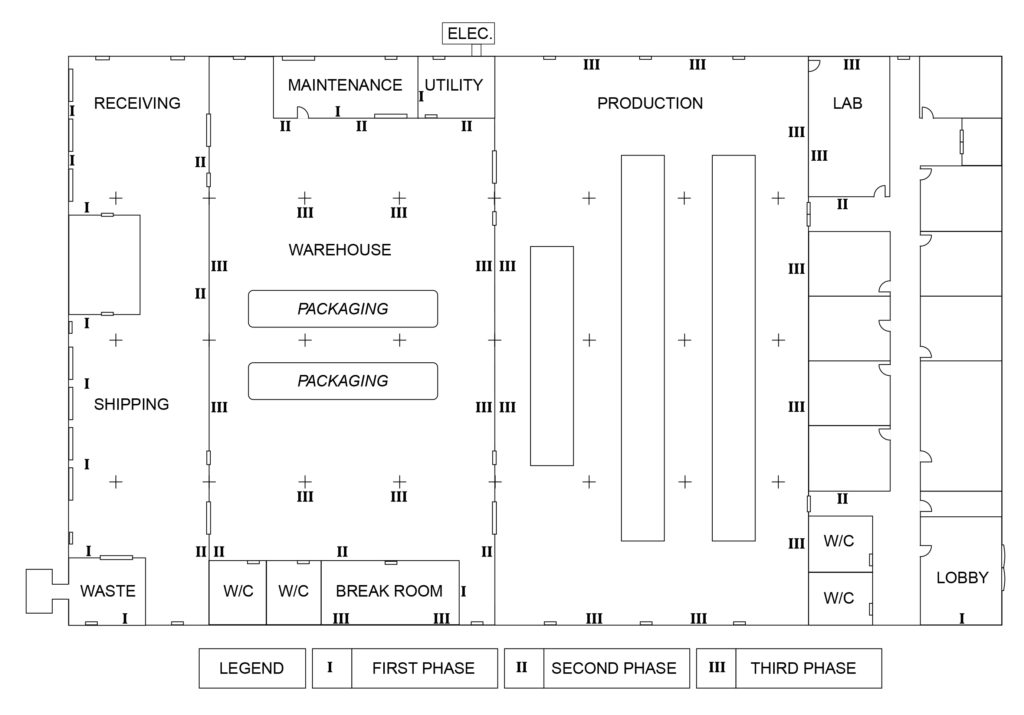
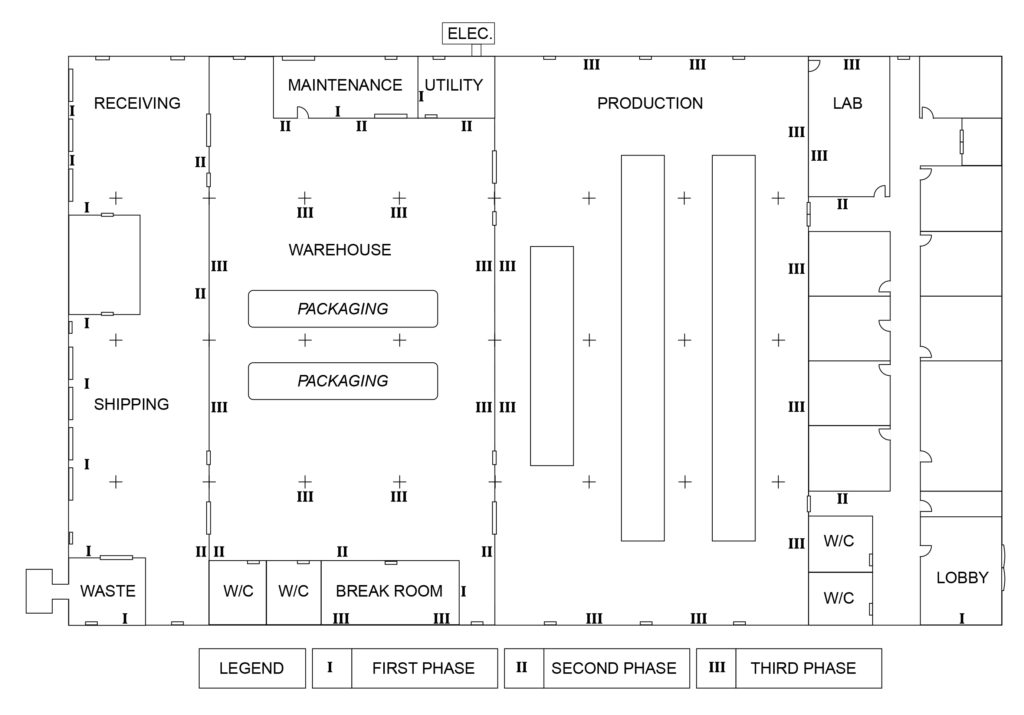
- Because of factors such as insect age and sex, room temperature, humidity levels, and competing attractions, about a third of the flying insects will ignore a black light source for a short period of time.
- Note: For best results, vertical wall mount Insect-O-Cutor® units should be located at elevations of no lower than one foot above the floor and no higher than four feet above the floor (the distance from the floor to the bottom of the unit).
- Elevators and stairwells form natural chimneys through which flying insects can reach upper story areas. An Insect-O-Cutor® wall mount unit should be positioned in each stairwell between the main and second floors, as well as between the main floor and sub-floor. An interception unit should also be placed in the vicinity of elevator openings on the sub-floor and the main floor.
Shop our selection of replacement black lights and pest control products
Frequently Asked Questions
Why use the unfiltered white bulb (BL) and filtered blue bulb (BLB) combination?
This exclusive BL and BLB combination ensures the highest level of flying insect attraction. Pairing a bright, unfiltered white bulb with a filtered blue bulb reduces the visible light that can act as a repellent and maximizes the amount of insect types attracted to the unit. BLB bulbs were tested and found to have an increased attraction from agricultural insects and pests.
My bulbs are lit, why do I need to change them?
A bulb that is still lit may not be doing the job you need it to. Black light (UV) bulbs are most effective when new. They lose their ability to attract insects long before they actually burn out. UV light is invisible and while the bulbs remain lit the UV producing phosphor only has an effective life of 7000 hours or about 9 months.
When should I change my bulbs?
It is essential to replace bulbs at least annually. Most users choose to change their bulbs in the spring, which is the beginning of the insect season. Each bulb comes standard with a year/date label for audit compliance, but also to aid in yearly replacement of bulbs.
What are Shat-R-Shield® bulbs and why upgrade?
Shat-R-Shield developed a fluorescent bulb with a specially formulated coating for black lights. This unique safety coating allows the critical UV wavelengths to penetrate and attract flying insects while special UV stabilizers prevent degradation. In case of accidental breakage, the coating will contain all glass shards. Safety coated bulbs are required to be used in areas with open or exposed food-grade product per FDA Food Code Sections 6-202.11; USDA Food Safety and Inspection Service, Chapter 5, Section 1. Safety coated bulbs also protect the employee if a bulb should break during usage or when changing bulbs.
How large of an area will an Insect-O-Cutor® flytrap cover?
Coverage by a particular flytrap depends upon many factors. Among these factors are: types of insects; competing light and other attractions; air temperature and movement. A general rule of thumb is to locate Insect-O-Cutor insect traps and electronic fly killers so that insects need not be attracted more than 35 to 40'.
Is there much maintenance required for flytraps?
Other than lamp replacement (which should be performed at least annually), Insect-O-Cutor's should be cleaned periodically. This constitutes brushing debris from the grid kill area, emptying the collection drawers, and wiping exterior surfaces with a dampened cloth.