Enhance workplace efficiency and eliminate waste through a structured five-step approach
5S is more than a program, it is a comprehensive system for organizing spaces so work can be performed efficiently, effectively, and safely. This system focuses on putting everything where it belongs and keeping the workplace clean, which naturally promotes a safer workplace with more efficiency.
When implementing a 5S system, it is important to remember to start small. Start with a pilot project to get a feel for if/what employee training is needed—how to implement the system, how to track progress, and how to celebrate success.


Step 1: Sort
Separate tools that are needed to get the job done and remove everything else. Sorting helps minimize cross-contamination and cross-contact by separating food-contact and non-food-contact items.
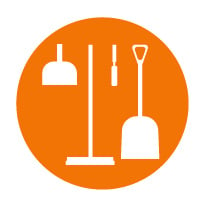
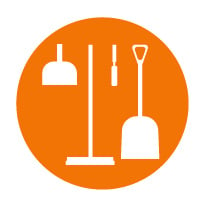
Step 2: Set in order
Reduce the need to be away from the workstation by placing all relevant tools within reach of operatives. Color-coding can be introduced to keep food-contact and non-food-contact items in separate zones and to keep allergens apart where needed. Shadow boards can be used to give every tool a place.
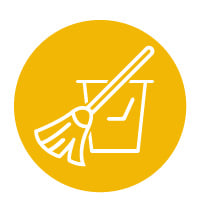
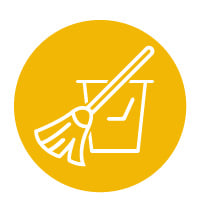
Step 3: Shine
Keep tools, machinery, and the work area clean to maintain safety and order in the workplace. Routine cleaning within your facility can help spot leaks, cracks, or misalignments, reducing the risk of equipment failure, safety hazards, and loss of productivity.
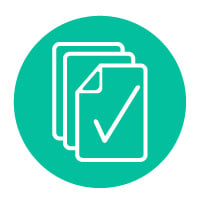
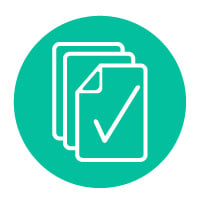
Step 4: Standardize
Introduce shadow boards and write standard operating procedures (SOPs) to create practices that will ensure the maintenance of the steps you have already taken. The process should have a natural flow and be more efficient.
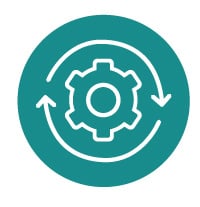
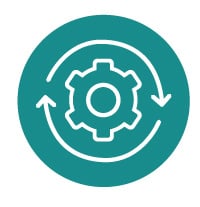
Step 5: Sustain
Stay consistent and constantly review standards with daily, periodic, and change-only checks.
Adding Visual Aides
Incorporating signs, labels, safety tapes, floor markings, and shadow boards are effective ways to visually communicate throughout a facility and maintain a successful 5S system.
Signs & Labels
Help increase awareness and communication - customize your safety sign
Identify specific areas or items.
Ideal for marking aisles, hazard boundaries, and color-coded areas.
Improve safety and speed up processes by extending the life of the equipment and eliminating missing tools.
Need help implementing a 5S System?
Contact our Product Specialists at sales@nelsonjameson.com, call 800-826-8302, or take our specialized survey!

