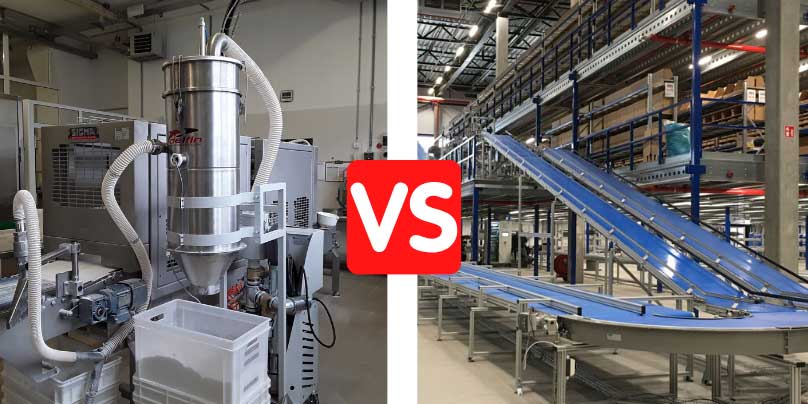
Selecting conveyor systems that are flexible, minimize waste, and ensure the integrity of transported products is vital for optimizing production efficiency. The market offers a diverse array of conveyor systems for integration into your production line, each with its unique features. Choosing the right solution is critical to prevent contamination of products and streamline the production process. While traditional conveyor belts efficiently move large quantities of powders, granules, and solids, they have drawbacks such as requiring significant installation space, exposing products to external contaminants, and being challenging and expensive to sanitize. Pneumatic conveyors provide an alternative solution, utilizing a closed airtight system to prevent product dispersion and contamination risks. This article delves into the working mechanisms of pneumatic conveyors, offering insights into their advantages, such as low maintenance costs, reduced contamination risks, prevention of product de-mixing, and enhanced flexibility compared to traditional conveyor belts.
How Conveyer Belts Work
Conveyor belts are devices used to transport powders, granules, and solids that can move large quantities of product, keeping it intact. However, they require a great deal of installation space in the production department,
expose the product to external contamination during transport, and are costly and complicated to sanitize and service.
Pneumatic conveyors allow you to transfer powdery, granular, or solid material from one place to another via vacuum. The completely closed airtight system prevents the product from being dispersed into the air and eliminates the risk of contamination. They can carry out various functions that go beyond simply transferring material between two places.
There is the option of having several product pick-up or destination points, even if they are far from each other, for a single conveyor. The product can be sifted before or after being conveyed and the conveyed material can be dosed both by difference (from the pick-up point) and by accumulation (at the discharge point).
Pneumatic Conveyance: How It Works
Pneumatic Conveyors: Flaked Parmesan
Your Solution for Conveying
To find the best solution for your material conveying needs, you must consider the transport features you require, as well as evaluate the important features in both systems, including:
Machine Maintenance Costs
- Conveyor belts require continuous maintenance, as there are numerous moving mechanical parts. In addition, a small portion of the transported material falls off the belt, which builds up and can cause costly machine downtime
if not constantly checked and removed.
- Pneumatic conveyors have no moving mechanical parts in contact with the product, only use a vacuum to convey the material and, therefore, do not require constant maintenance.
The Risk of Contamination
- Conveyor belts are open systems that allow foreign objects to contaminate the product being conveyed.
- Pneumatic conveyors are closed airtight systems that do not allow foreign objects to come into contact with the product being conveyed.
The Risk of the Product De-Mixing or Breaking Apart
- On conveyor belts, the material is in constant contact with surfaces, making it possible for the product to be ruined.
- On the other hand, inside pneumatic conveyors, the material is transferred via air, floating through the piping, thus minimizing any contact with surfaces. By using specific conveyors, it is also possible not to de-mix the product during the pick-up, conveying, and discharge steps.
Flexible Use
- Conveyor belts are bulky, not particularly flexible systems that are difficult to move in the event their direction or location needs to be changed. Belts can easily carry heavy loads and can cover very long transport distances.
- Pneumatic conveyors are not bulky and can be installed quickly.
The flexible hose system makes it easy to move in the event the production department must be rearranged. If necessary, frames
on wheels can be set up to allow the suction hopper to be moved throughout the entire production area.
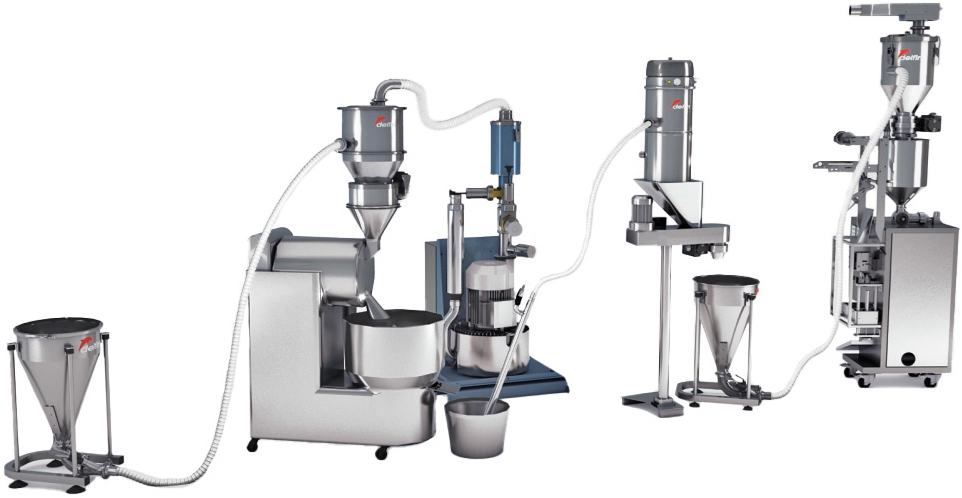
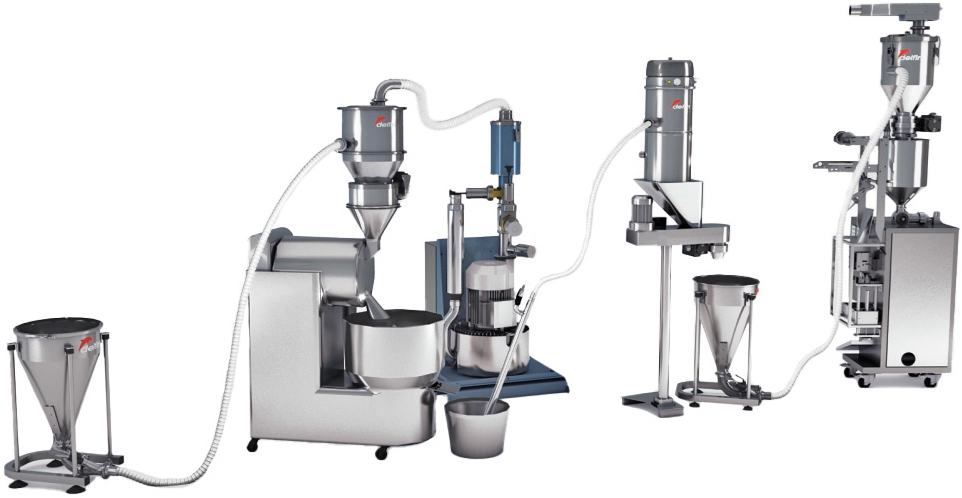
Let's talk! Contact our Product Specialists to discuss your plant needs and applications.