Detection of contaminants is a critical aspect of ensuring food safety, especially with stringent government regulations. The use of metal detectors is increasingly vital to identify and reject harmful objects, contributing to enhanced Hazard Analysis and Critical Control Points (HACCP) and Good Manufacturing Practices (GMP) programs. This comprehensive approach extends to a wide range of metal-detectable products, from safety supplies to processing tools, ensuring the integrity of food products. The smallest detectable foreign object varies based on factors like material, line speed, and moisture content, with the detector head's height being crucial. Calibration is a key process, involving setting thresholds based on contaminant size and collaborating with the metal detector manufacturer. Regular testing of calibration is essential to prevent larger contaminants from bypassing the detector and compromising product safety. Metal-detectable products, often colored blue for easy visual detection, employ unique manufacturing processes, such as embedding metallic pigments in plastics or enclosing stainless steel ball bearings in items like earplugs, ensuring detectability throughout the entire product or specific parts. Understanding the calibration process and utilizing metal-detectable materials contribute significantly to maintaining food safety standards.
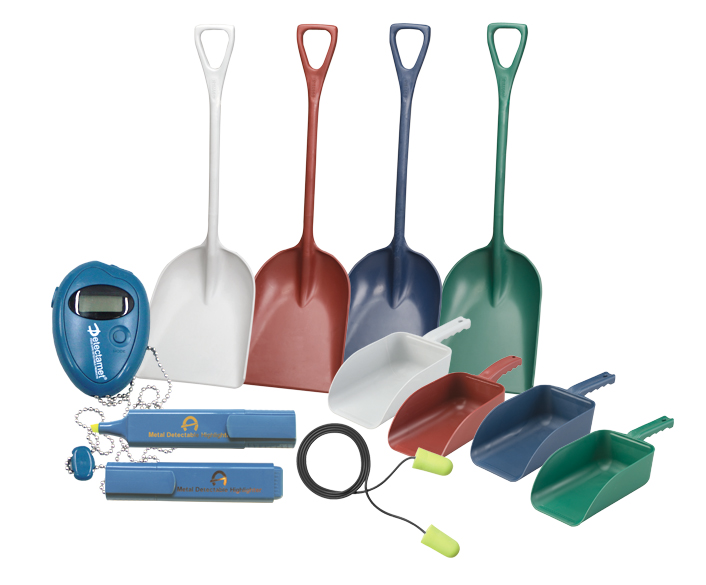
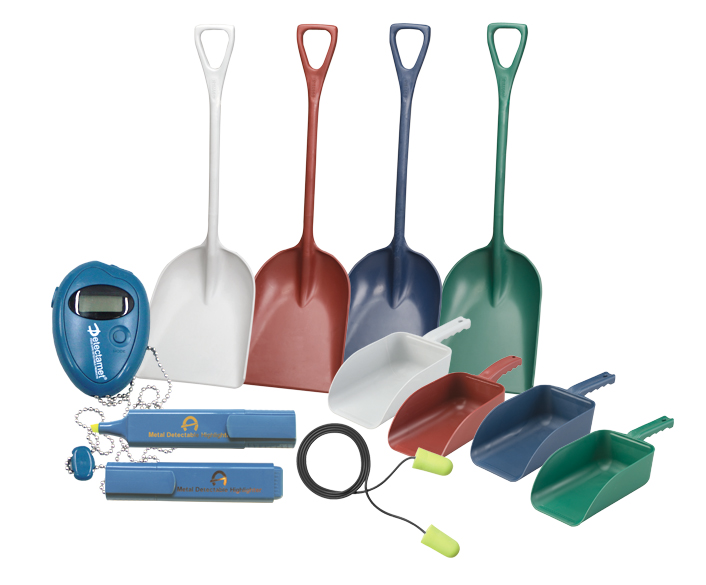
Metal Detector Calibration
What is the smallest foreign object that can be detected by a metal detector?
This answer varies greatly. It is dependent upon the material of the contaminant itself, the speed of the line and the moisture content. The height of the detector head from the line is the most critical variable, as sensitivity decreases as height increases.
How do you adjust a metal detector?
Machines must be calibrated to the food they are processing and then set to a threshold, determined by the company, in regards to the size of the contaminant they want the detector to reject. The type of product passing through the detector (wet or dry), its size, and speed affect the setting.
The metal detector manufacturer can assist with calibration setup.
What happens if you don't test the metal detector's calibration?
If you don't test a metal detector's calibration, the metal detector can allow larger pieces of foreign contaminant to get through, compared to the threshold setting, threatening the finished product's safety.
How do you maintain metal detector calibration?
You want to periodically check calibration by passing a known calibration test tool under the unit to check for accuracy. These can be made of ferrous, non-ferrous, or stainless steel, and come in the form of rods, cylinders, balls, whips, cards and more.
Metal Detection Materials
Why are so many metal-detectable products blue?
Many metal-detectable products are colored blue for two reasons:
- Easy visual detection.
- It is the most common non-food color.
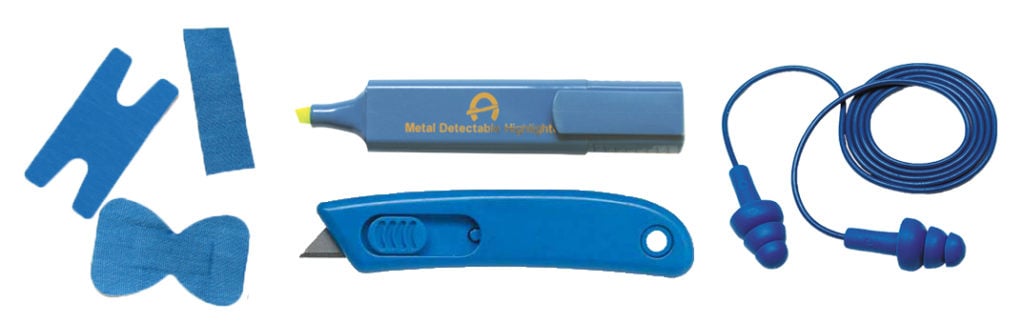
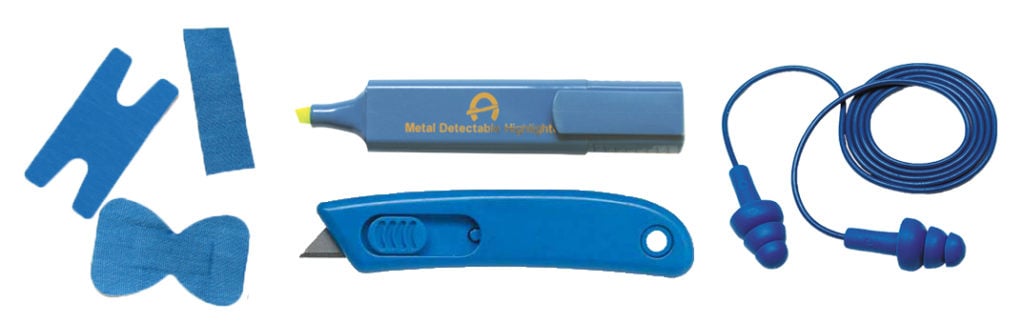
What makes tools and equipment metal detectable?
In plastic products such as scrapers, pens, and vinyl gloves, a unique manufacturing process involving the inclusion of a metallic pigment enables the plastic to be detected. In other products such as earplugs, a stainless steel ball bearing is enclosed in the plug to make them detectable.
What is the difference between embedded metal and impregnated material?
A product with embedded metal is only detectable if the product piece containing the metal goes through a detector. With a product that is impregnated, the entire piece has fine metal particles throughout, making the entire piece, or parts of it detectable.
Shop our selection of metal detectable and x-ray visible products.