Learning Center

Every year, destructive and deadly dust-related fires and explosions affect a wide range of industries around the globe, including the food processing industry.
According to the 2021 Combustible Dust Incident Report Summary by Dust Safety Science, in the United States alone, there has been an average of 133 fires, 30 explosions, 39 injuries, and one to six fatalities per year (between 2016 and 2021).
To help manage dust-related fires, flash fires, and explosion hazards, the NFPA® introduced NFPA 652: Standard on the Fundamentals of Combustible Dust .
All facilities that handle or produce combustible dust, or particulate solids that may become dust, are at risk of a potential dust explosion. NFPA 652 defines combustible dust
This webinar provides crucial information on preventing and mitigating combustible dust hazards, emphasizing the potential dangers posed by fine particles in specific environments, including the risk of fires, explosions, and safety hazards for personnel. Enhance your awareness and knowledge of combustible dust dangers by watching the Dust Busters Webinar, led by industry-leading experts in dust hazard prevention. The webinar covers essential topics such as understanding combustible dust explosions, conducting site dust hazard assessments, implementing mitigation strategies, and addressing frequently asked questions. Tailored for individuals in plant operations, the webinar is particularly relevant for those in processing facilities, manufacturing plants, and similar environments prone to generating combustible dust.
Nelson-Jameson is your premier destination for personalized laboratory furniture, cutting-edge equipment, and comprehensive design services, catering to both domestic and international laboratory facilities. Our collaborative approach enables us to meticulously strategize every aspect of your lab space, offering expert guidance on cabinets, countertops, fume hoods, sinks, balance tables, safety cabinets, and an extensive array of other laboratory essentials. With a commitment to building bespoke, adaptable systems, our focus is on optimizing laboratory spaces for diverse applications. Whether you require state-of-the-art lab furniture, specialized equipment, or a complete lab design overhaul, Nelson-Jameson is your trusted partner in creating efficient and functional laboratory environments. Contact us to get started today!
In April of this year, OSHA - Region V - WI published a Local Emphasis Program (LEP) established for the purpose of scheduling and conducting inspections within the Food Manufacturing Industry (click here for full details.)
The launch of the LEP allows for greater “outreach, education, training, and enforcement activities.” For many reading this, this specific LEP may not pertain to your facility. However, the rationale behind this special program is something that we can appreciate across the food industry. Reminders like this in our busy, hectic schedules can do a lot “to encourage employers to take steps to identify, reduce, and eliminate hazards associated with exposure to machine hazards during production activities, and off-shift sanitation, service, and maintenance tasks.”
Let’s face it, a food processing
Safety is a major concern in any workplace, especially when working with machinery and equipment. This Lockout Tagout Buying Guide is your comprehensive resource to understand and implement lockout tagout procedures effectively, ensuring the safety of employees and preventing serious accidents. Lockout Tagout (LOTO) is a critical protocol that prevents the unexpected start-up of machinery during service or maintenance, safeguarding workers from potential hazards. This guide covers various aspects, including the definition and use of lockout and tagout, the importance of hazardous energy control, OSHA requirements, and steps for complete OSHA compliance. Delve into the details of lockout tagout procedure steps, the responsible parties for LOTO, training requirements, and scenarios where lockout must be applied. Learn about different lockout tagout devices, their definitions, and uses, ranging from cable lockouts to valve lockouts, ensuring a thorough understanding of the tools available
This content highlights the advantages of switching from rigid plastic containers to Whirl-Pak® Bags in the sample collecting and storage process. The benefits include a significant reduction in plastic media waste, greenhouse gas emissions, water usage in manufacturing, overall hands-on time, and storage space. Additional advantages encompass lower shipping and disposal costs, along with puncture-proof, leak-proof closure tabs, guaranteed sterility, and easy identification. The information is backed by a case study conducted in April 2022 by Nasco Sampling LLC. The content also provides a step-by-step guide for implementing the switch, addressing considerations such as raw material and finished product testing, informing purchasing and disposal services, capturing team concerns, and setting up product and testing stations. The Whirl-Pak® Bags meet federal regulations and comply with standards set by FDA, USDA, HACCP, and EPA. For further information or assistance in transitioning
Selecting conveyor systems that are flexible, minimize waste, and ensure the integrity of transported products is vital for optimizing production efficiency. The market offers a diverse array of conveyor systems for integration into your production line, each with its unique features. Choosing the right solution is critical to prevent contamination of products and streamline the production process. While traditional conveyor belts efficiently move large quantities of powders, granules, and solids, they have drawbacks such as requiring significant installation space, exposing products to external contaminants, and being challenging and expensive to sanitize. Pneumatic conveyors provide an alternative solution, utilizing a closed airtight system to prevent product dispersion and contamination risks. This article delves into the working mechanisms of pneumatic conveyors, offering insights into their advantages, such as low maintenance costs, reduced contamination risks, prevention of product
5S is more than a program, it is a comprehensive system for organizing spaces so work can be performed efficiently, effectively, and safely. This system focuses on putting everything where it belongs and keeping the workplace clean, which naturally promotes a safer workplace with more efficiency.
When implementing a 5S system, it is important to remember to start small. Start with a pilot project to get a feel for if/what employee training is needed—how to implement the system, how to track progress, and how to celebrate success.
5S IS A FIVE-STEP PROCESS:
- Sort: Separate the tools that are needed to get the job done.
Remove everything else. - Set in Order: Place all relevant tools within reach of operatives and reduce the need to be away from
Oterra™ Natural Colors for candies and confectioneries provide a color palette even Cupid would adore! As the world’s leading supplier of natural colors, Oterra continues their dedication to applying the goodness and purity of nature to our food. Their advanced technology and mission promotes every step -or arrow!- in the right direction to suit various applications with no compromise on quality or safety, therefore offering a wide product range.
If you are looking for natural colors to help create products for the day of love, there are several Oterra products available. Each offer a full spectrum of colors and natural ingredients to help produce the best color for your specific application.
- I-Colors®: Colorful, instant powders that plate well and hydrate easily.
- Promotes resilient coatings for easy, trouble-free panning.
The Incoplas® LED Hybrid Hazloc, from Shat-R-Shield®, is a durable multi-purpose and corrosion-resistant LED lighting solution that can be used in heavy industrial applications where hazardous location lighting is required.
Features
- Specifically designed to withstand moisture, dust, chemicals, salt spray, and harsh environments.
- Uses thermally conductive engineered polymers to extract heat away from the light source and offer consistent heat dissipation.
- Significant weight reduction over comparable aluminum fixtures.
- Multiple mounting options to choose from.
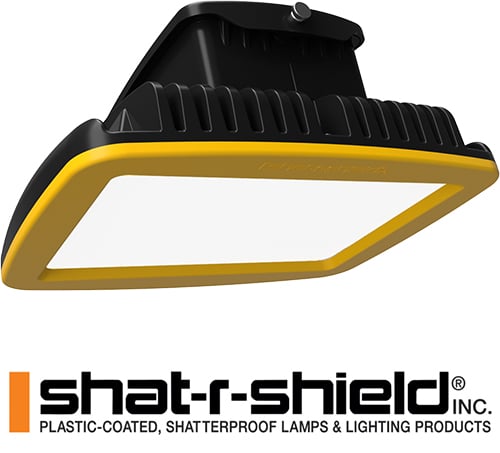